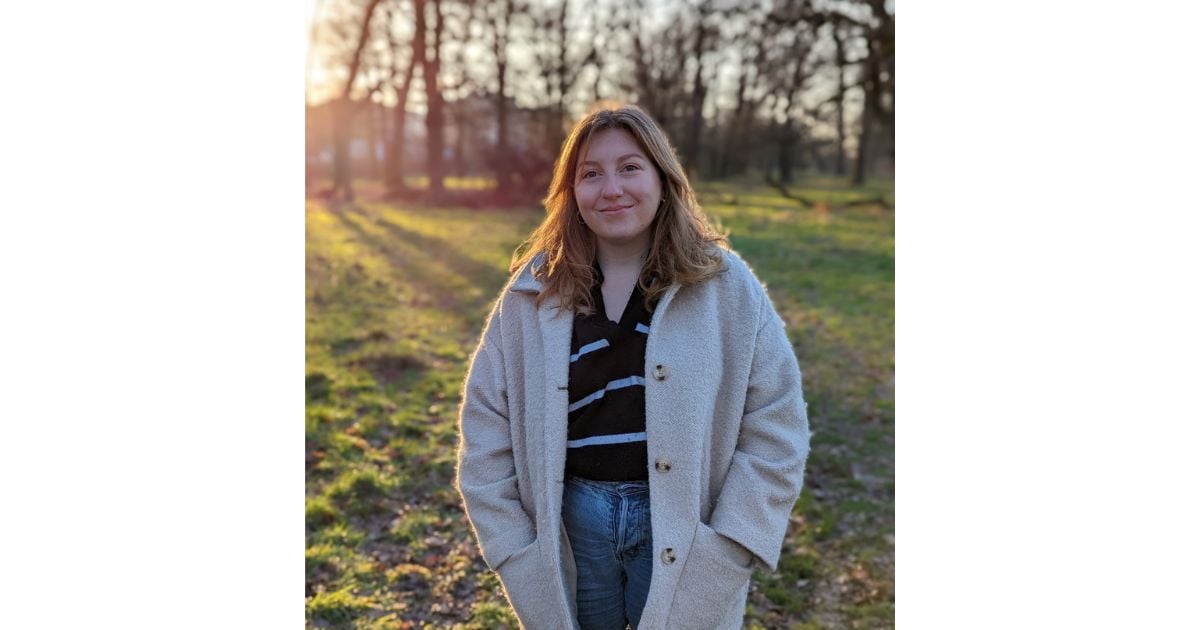
Beth Howell
Beth has been writing about the environment and climate change for over four years now – with her work being featured in publications such as The BBC, Forbes, The Express, Greenpeace, and in multiple academic journals.
Plastic collection is an essential tool when it comes to helping the environment — but what happens to this waste once it's collected?
This is a common question we get at CleanHub, and it's one of the key reasons why we developed our detailed track-and-trace software. It's important to know what happens to the waste we collect from households, where it goes, and how it's treated.
Want to learn more? We've outlined everything you need to know about this software in the article below.
What's on this page?
01 | How does the Cleanhub system work?02 | The track-and-trace process explained
03 | Why is this data so important for our mission?
04 | Why we've chosen this approach
05 | How the plastic credits are distributed
06 | FAQs
How does the CleanHub system work?
We work with a number of collection hubs around the world to recover plastic from vulnerable areas — that's a lot of people working towards the same goal.
To make sure we're accurately recording the amount of waste collected, all of these hubs use our track-and-trace technology to record the volumes.
This software has been developed by our in-house team, and does what it says on the tin — it tracks the waste from collection to final recovery, where the material goes through a laboratory.
To elevate this process further, we've also developed an app that makes the data-logging process more seamless for our collection teams on the ground. Not only does this help us maintain transparency, but it makes the process much easier for workers.
Want to learn more? Find out how we work together with brands in our comprehensive guide The Benefits of Partnering with CleanHub.
The track-and-trace process explained
Our wonderful in-house team has spent countless hours developing and perfecting our trash-tracking software.
We wanted this system to be thorough, efficient, and effective to bring more transparency to our operations — but also to make the collection more time-efficient for the teams on the ground.
Here's how the process works.
1. Collecting the plastic
The plastic recovery journey starts differently depending on the collection method our teams use. In most cases, we collect plastic waste directly from households, but we also carry out beach cleaning operations from time to time.
For this explanation, let's assume we're using our primary recovery method: household collection. Here's how our trash-tracking software works:
- Scan the QR code: The collection crew scans a QR code on the door, which opens our app and registers that they have now checked in to a specific location to collect waste.
- Measure the waste: Once the homeowner hands over the waste, the collectors put it on a small scale. The collection crew also takes a picture of the waste bag on the scale in that location. This image doesn't directly show what material is in the bag, but it allows us to understand which weight distribution is normal. The content of the waste bag is not too crucial at this stage because it can still be mixed with household waste that will be sorted later.
- Input additional information: Along with the bag’s image, we resolved the geo-location to make sure the waste was collected where it was supposed to be collected. The collection crew also registers the weight displayed on the scale so we can cross-check these values.
- Continue collection: The collection crew continues the route until they’ve been to all households. Our app aggregates the sum of collected waste.
- Transport waste: Once the route is completed, the waste goes into an MRF — a Material Recovery Facility. At this stage, all the waste is weighed on a larger scale. Usually, the truck that carries the waste is weighed — this way, we get a second data point that we can cross-compare to the collected volumes en route.
If there is too much of a deviation between the weight measurements from the household collection and the MRF measurement, we know that something went wrong. If it is way more, it means that someone is potentially trying to sneak in waste along the way. If it’s a lot less, we also know that something went missing on the way.
Whether the waste is sourced from household collection, a cleanup, a river barrier, or a scrap dealer, we always follow this process.
2. Sorting the trash
Once the trash has reached the facility, it's time for the crew to sort out it into recyclables and non-recyclables — recyclables will be reused, and non-recyclables will be sent to a co-processing facility to be turned into fuel.
This material is either baled or put into big packs for storage, individually registered on our app again, and later transported to their next stage (recycling or co-processing plant).
Why do we need to register the waste again? For the waste management nerds: we’re monitoring the mass balance. In simple terms, it's just so we know how much material goes into a sorting process at each stage, and what the output is.
Since we also know where the waste was sourced, we can learn over time what standard behavior looks like and what anomalies look like. For example, if there are suspicious data registrations, we can immediately intervene and ask for more information.
3. Sending the trash to the facility
The crew loads and secures the material onto a truck, and sends it to one of our co-processing partners (while recyclables are sent to a nearby recycling facility).
On departure, the truck goes over a weighing bridge again, and our collection partners register the net weight of the truck. At this point, we know exactly how much plastic waste left the location (including the geo-location again) and where it is supposed to go.
We also know if there is more waste loaded on the truck than the sorting center had in stock, which would again be a sign that there is waste put on the truck that is not supposed to be there.
On arrival at the co-processing center, the truck goes over a weighing bridge again. At this moment, we cross-check the volumes booked at the sorting center and those that arrived at the co-processing plant.
To some, this level of stringent checking might seem excessive, but it means we can be sure that we're providing accurate data to the brands that fund the plastic collection. Transparency is key.
4. To the lab and beyond
Before getting to work on the trash, the engineers at each co-processing location take a sample of every truckload that arrives. They observe three key values in the waste — the moisture content, the calorific value, and contamination. And here's why:
Moisture content
All waste has a bit of water in it. However, co-processors can’t feed material to the kiln that is too wet, as it prevents them from reaching the necessary temperatures during incineration. This means we need to reduce moisture levels in the waste as much as possible.
This is also important for us though. After all, we want to issue plastic credits — not water credits.
We pay our collection partners based on the dry-waste weight. So if there is a truckload of 10 tons of plastic going into co-processing with a moisture content of 10%, we pay for a collection of nine tons. At the same time, we also only sell nine tons — or we only issue nine plastic credits, to be more precise.
Once we know the final dry-waste volume, our app splits it among all brands that support the specific project that collected the waste.
Calorific value
The co-processor cares about calorific value because it helps create the fuel needed to reach the temperatures in the kiln.
For us, it's yet another data point that helps prevent fraud. Different types of plastic have different calorific values plastic, meaning we're able to spot any anomalies. While not super precise, massive deviations would again show that it's not the material we wanted to reach the plant.
Contamination
The lab looks for specific contaminants in the waste — especially chlorine. Chlorine is part of a particular plastic type called PVC. This chemical is problematic for two reasons: the toxic emissions from burning it and chlorine in high concentrations would eventually shut down the plant because it can block the kiln.
For us — you guessed it — this is yet again another data point we can use to make sure there are no deviations in our collected waste.
Finally, after all these checks, we receive a co-processing certificate that guarantees that the waste will be destroyed through co-processing. Once all this documentation is in place, we count the waste as verified and collected.
Why is this data important for our mission?
When it comes to collecting plastic waste, transparency is key — and this is the main reason we've developed our trash-tracking software. It clears up any uncertainties for us, our brand partners, and the collection hubs we work with.
Each person handling the collected waste along the different stages of the process is part of our digital ecosystem. Like any ecosystem, things can get a little complicated, so it's important for us to be as transparent as possible — which is why each brand that partners with us also has access to its own impact report, outlining all of the recorded data about its plastic recovery.
It's our responsibility to protect all upright collection partners, brand partners, and our own credibility — and to catch fraudulent behavior if it happens. The only way to do that without spending massive amounts on auditing services (which would dilute money away from true impact) is through data and ever-increasing pattern recognition in that data.
Transparency has never been more important in the environmental space, as more countries around the world implement greenwashing legislation. Any brands claiming to fund plastic recovery, reduce emissions, or implement any other environmental initiatives need to back up their claims with data — and that's exactly what we're doing with our track-and-trace software.
A note on data collection
As technology continues to grow at a rapid rate, there is a lot of concern around data collection — and rightfully so!
That's why we want to highlight that we only collect processing data from collection hubs, not personal data.
We have deep-rooted trust with our partners — and they're fully aware of the data we’re collecting.
Why we've chosen this approach
We believe that this is the most comprehensive and inclusive approach to plastic recovery, from a monitoring and scalability point of view.
Waste management needs to happen locally to overcome the many cultural hurdles that many communities face in low-income areas. These communities, and their local entrepreneurs, don’t need patronizing — they need access to capital.
In terms of data, this approach is something we think sets us above other plastic credit suppliers. By providing this level of detail, brands that partner with us can see where exactly the plastic we collect is going. And with greenwashing on the rise, this level of transparency is vital.
Brands need to know that the plastic we collect isn't simply going to landfills to generate more emissions and pollute the environment — it's being fed back into the economy.
At CleanHub, we receive an average of 59 data points for every ton of verified plastic. All of these points form a bigger picture, which tells us what’s going on and whether this is legitimate or not.
You can monitor all these data points with full transparency on our technology page.
Our impact
At CleanHub, we want a world free of plastic pollution — and we’re making this happen by collecting all kinds of waste from coastal communities, preventing it from being openly burnt, dumped, and reaching waterways.
So, how much waste have we collected so far? Let’s break it down.
As of May 2024, we’ve collected 9,529,203 kilograms (kg) of waste — all financed by our amazing brand partners. That’s the same weight as 317 humpback whales!
This is mainly made up of plastics but also contains paper, cardboard, and wet waste. Our collection hubs estimate that roughly 30% of the waste we collect and sort is recyclable plastic, which is then sold into the recycling process.
To make sure our projects have additionality — meaning they wouldn’t have happened without our financial support — we only incentivize and pay for non-recyclable waste. So far, we’ve collected 5,077,792 kg of non-recyclable certified waste, measured as ‘net-dry’ plastic waste where the moisture contents are deducted from the final weight.
On top of this, one of our key goals is to bring more transparency to the waste industry, which is why we also partner with waste managers beyond plastic credits, inviting them to use our technology to track collections and manage their operations.
Through this partnership, an additional 343,875 kg of waste has been tracked using CleanHub’s technology, including mixed municipal solid waste or pre-sorted waste.
Summary
The entire process — from collection, sorting, aggregating, and final testing — takes time, but this level of detail is paramount in an industry as new as plastic credits.
And with greenwashing legislation on the rise around the world, our track-and-trace system has never been more important.
Want to reduce your business’s plastic footprint? Let’s talk. Our in-house experts can help you figure out which plastic recovery plan best suits your business's needs.
FAQs
Where can I see CleanHub's tracking data?
You can find a real-time feed of the data coming into our system from all collection hubs on our technology page. Each event on the feed represents collected plastic being registered, sorted, and responsibly disposed of.
What are the benefits of plastic collection data?
Collecting data on our plastic recovery efforts benefits everyone involved. It helps us keep track of the plastic we've recovered, making sure to check for any anomalies or issues along the way. It also helps the hubs that we work with understand the volumes of trash they're working with.
Above all, it provides a window for the brands that partner with us and fund these plastic recovery efforts — a chance for them to see how much waste is being recovered on their behalf, and peace of mind that we're being transparent and honest.
What verifications does CleanHub have?
CleanHub was the first plastic credit system to be verified by industry leaders in auditing environmental impact TÜV SÜD. With this certification in place, users can be assured that we are authentic, transparent, and trustworthy with our plastic recovery efforts.
Find out more about this by visitng our page on the TÜV SÜD verfication.